Rayleigh-Ritz Autoencoder
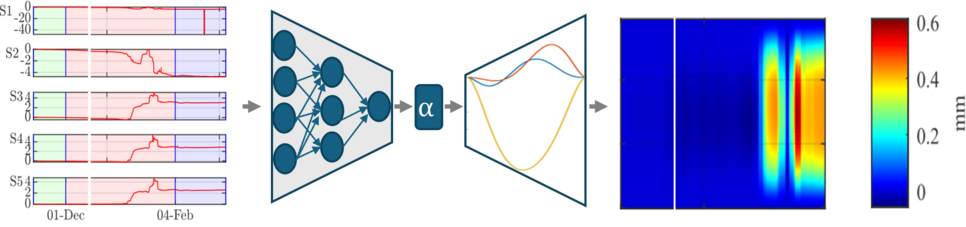
The Rayleigh-Ritz Autoencoder (RRAE) is an architecture for unsupervised scientific machine learning. The RRAE combines a machine learning tool, the autoencoder, with a classical engineering tool, the Rayleigh-Ritz method. The RRAE consists of an encoder, which is a trainable neural network, and a decoder, which can be considered as a pre-trained neural network, that implements the values of the synthesised admissible functions. This architecture, combined with the automatic synthesis of admissible functions, provides a machine learning framework that allows the exact fulfilment of generalised constraints.
Digital Twin for Ground Improvement
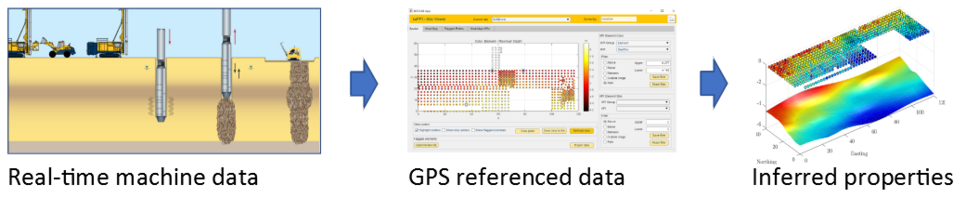
This project developed a digital twin for monitoring ground improvement processes for deep vibratory methods. This is part of implementing a digital construction site. The goal is to improve quality assurance and the monitoring of each produced element; since safety is a key measure in Geotechnical Engineering. The system permits the domain experts to explore the data on their own, without the need for a dedicated data scientist. This will leads to a significantly reduction in time required for post-production quality control measures.
Evidence Based Hypothesis Testing
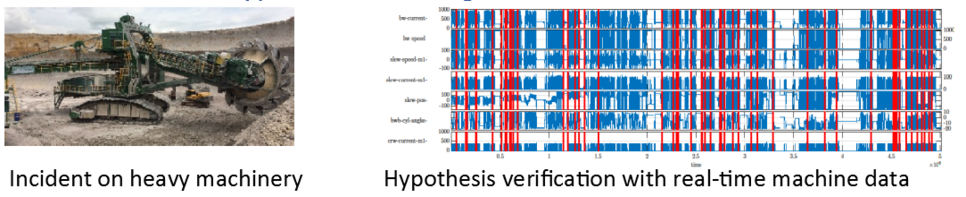
The extremely high cost of lost production time with heavy plant and machinery makes incident analysis a major issue in claims management. The digital twin maintains a historical data base for the real-time machine data over long periods with high temporal resolution. In this project a rule execution engine was developed to automatically search the historical data for specific conditions. In this manner hypotheses can be formulated and tested to see if there is a causal relationship to the incident.
Discrete Mathematics and Structural Monitoring
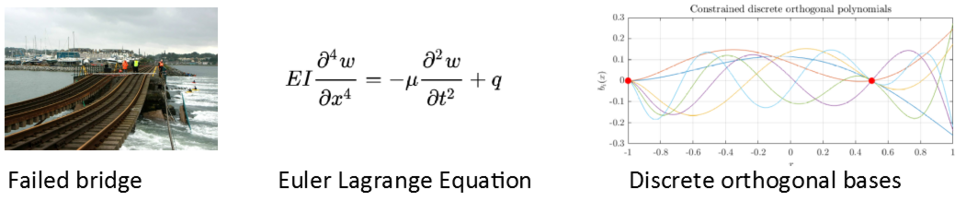
This project involved the analysis of sensor data from the monitoring of structures. A new approach was developed to solving the inverse problems based on discrete orthogonal basis functions with constraints. These permit the highly efficient solution of the inverse problem. Furthermore, it enables the identification of failed assumptions, a particular important issue in safety relevant applications. This demonstrates the increasing application of advanced mathematical concepts in engineering.
Applied Mathematics in Signal Processing

This project is focused on developing and applying mathematical methods to analyze measurement data. One method is used to detect discontinuities in the n-th derivative, which can be later used as break points for spline modeling of the data. Another method focuses on separating periodic signals having an aperiodic trend, using the method of variable projection. The periodic portion of the data is modeled by trigonometric functions, whereas the aperiodic portion is modeled by B-splines. Both of these methods make heavy usage of B-splines when modeling data, since they perform much better when compared to other basis functions.
Unsupervised Machine Learning for Time Series

For anomaly detection in safety-relevant applications of heavy machinery, an unsupervised machine learning model was developed. This model can capture anomalies in time series data that cannot be detected using statistical methods. Additionally, machine learning was combined with the meta-heuristic of the group of genetic algorithms to optimize the initial settings, hyperparameters, of the model to make the properties of this generic model self-adaptive to data with different characteristics.
Model-based Condition Monitoring (MBCM)

This project explored new ways to fuse knowledge-based modelling and machine learning for condition monitoring. Instead of integrating process-specific knowledge, generic analytic methods developed at the chair are combined with learning algorithms. In detail, the potential of polynomial discontinuity measures and discrete orthogonal basis functions to enhance autoencoders is demonstrated. This results in models with reduced training data requirement and higher physical consistency that work in an unsupervised manner.
Pavement Texture Analysis for Tire Test Benches
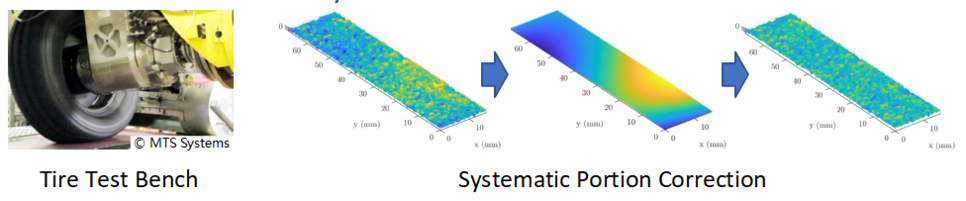
Topics like fuel consumption, handling and safety are the top priorities in the development of tires. Therefore special tire test benches are used to thoroughly test the tires. In order to achieve realistic modeling the surface of the test bench imitating the road should be close to real road pavements. This project developed an alternative data preprocessing procedure for the characterization of belt coatings used in tire test. The developed method is an adaption of ÖNORM ISO-13473 especially suitable for belt coating samples.
Condition Monitoring and Motion Modelling
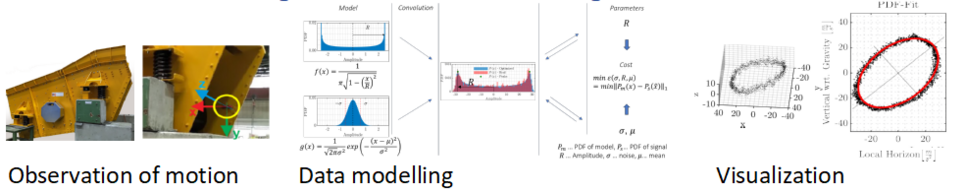
Industrial vibrating screens are used in the field of secondary raw material processing. The efficiency of such a screen depends heavily on the movement that the screen makes while material is being processed. In this project the motion of a sieve was monitored with a new developed sensor system including a 3-axis accelerometer. Since the orbital data is composed by a sine and Gaussian noise, the probability density function of both components were used to model the data. The separation of the two components enables the acceleration amplitude to be determined and further the displacement to be derived.
Sensor Modelling and Calibration
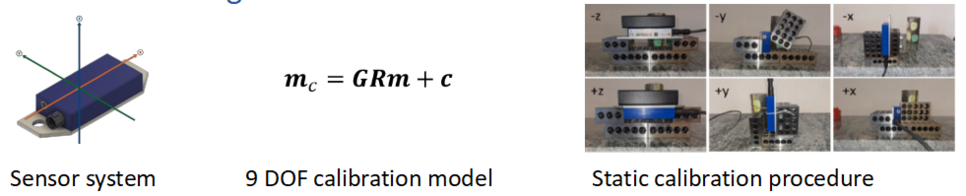
A newly developed sensor systems including multiple sensor elements as well as a processing unit require suitable calibration models in order to obtain undistorted sensor data. A calibration model was found with which the accelerometer within this system can be calibrated for 9 degrees of freedom. It corrects the measurements for the gain and the offset as well as for the 3D rotation of the sensor element within the sensor housing wrt. the outer reference aluminium base plate. The calibration parameters can be determined after 6 static measurements in orthogonal directions and a non-linear least squares optimization.
Detection of surface cracks in railway rails
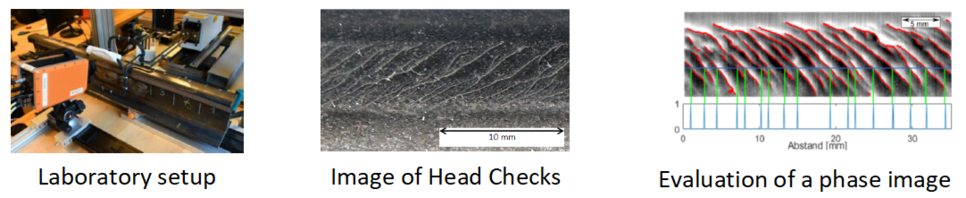
Railway rails are exposed to cyclical stress in the contact zone between rail and wheel causing so called rolling contact fatigue (RCF). In this project inductive thermography was used to detect Squats and Head Checks – two common types of surface defects caused by RCF. Phase images where used to characterize Head Checks and estimate the depth as well as the penetration angle of Head Checks.
ANSYS simulations of inducting thermography

Simulations are a useful tool to get a better understanding for physical mechanisms during a specific process. At the chair of Automation ANSYS is used to simulate inductive thermography, which is a non-destructive testing method. The eddy current and temperature distributions are simulated around surface cracks, in order to optimize the testing method.
Delamination and impact defects in CFRP specimen
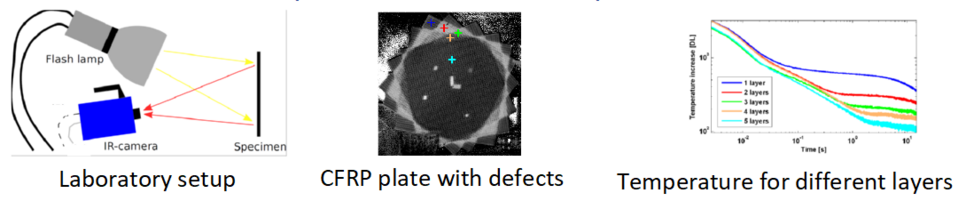
Delamination during production and impact defects caused during the live cycle of CFRP plates are two types of defects which can be hardly detected by visual inspection. Flash thermography is a method for non destructive testing which can be used to detect these defects. With this method it is possible to locate the defects and estimate the depth in which the delamination occurs.